Whether you have a manufacturing project or want to convert your idea into tangible realities then prototyping is the key that unlocks the doors of innovation. As inventors, engineers, and designers, we strive to craft functional and efficient prototypes that pave the way for groundbreaking products.
Both aluminum and titanium are wonderful options when choosing a suitable material for your project. As both are harnessed in various manufacturing sectors across the globe for making diverse products. Before you choose between these two excellent materials, it is advisable to comprehend their characteristics to make an informed and right decision.
This article will discuss the properties of titanium and aluminum, their pros and cons, and their different applications. Follow closely as we dive in!
Understanding Titanium
Titanium is a remarkable metal that has garnered immense attention for its unique characteristics and properties. These attributes make it a preferred choice to be used in various industries including prototyping. Let’s explore titanium and understand why it stands out as a heavyweight contender as a prototyping materials.
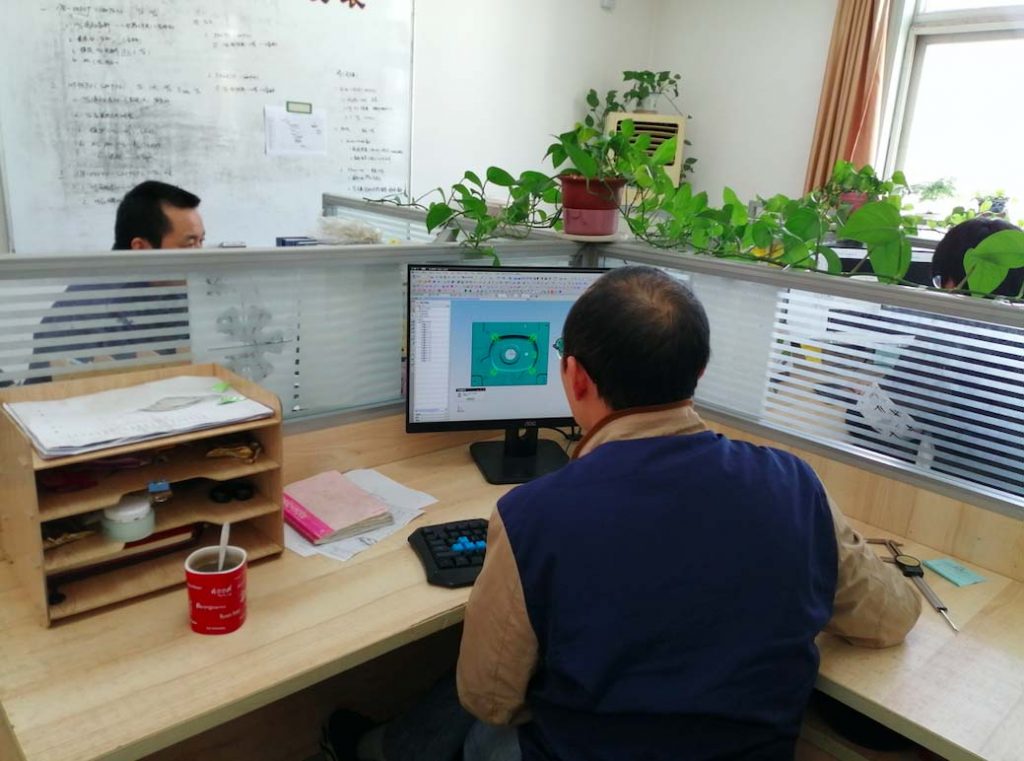
Characteristics and Properties of Titanium:
Titanium offers exceptional set of properties that manufactures can benefit from in their product fabrication. Some important of them are discussed below:
Lightweight Marvel:
Titanium boasts an impressive low density. Due to which it is exceptionally lightweight compared to many other metals. This feature is crucial for prototyping applications where weight reduction is a key priority.
Unmatched Strength:
Despite its lightweight nature, titanium possesses outstanding strength and rigidity. That’s why it is preferred for creating prototypes that require durability and resilience.
Corrosion Resistance:
One of titanium’s most prized attributes is its exceptional resistance to corrosion. It forms a protective oxide layer when exposed to oxygen. Which safeguards it against rust and deterioration. That renders it adaptable to diverse environmental conditions.
Biocompatibility:
Titanium’s biocompatibility makes it widely used in medical and healthcare applications. Because titanium created prototypes for medical devices and implants are well-tolerated by the human body.
High Melting Point:
Titanium exhibits an impressively high melting point. It enhances its suitability for applications involving extreme temperatures.
Applications of Titanium in Prototyping:
Aerospace and Aviation:
Titanium’s exceptional strength-to-weight ratio has made it a staple material in the aerospace and aviation sectors. It is used for making lightweight yet robust components.
Medical Innovations:
In the medical field, titanium’s biocompatibility and corrosion resistance are invaluable attributes. These lead to the development of cutting-edge medical prototypes and devices.
Automotive and Sports Equipment:
Titanium’s ability to reduce weight without compromising strength has found applications in automotive parts and high-performance sports equipment.
Limitations and Considerations for Titanium Usage:
Cost Factor:
Titanium is relatively expensive compared to other metals. Which can impact the overall cost of prototyping projects. Cost considerations must be balanced against the benefits it offers.
Machinability Challenges:
Titanium’s high strength and low thermal conductivity can make it challenging to machine. It requires specialized tools and techniques. Which may add complexity to the manufacturing process.
Limited Availability:
Although titanium is a highly sought-after material. But its availability can vary regionally. That can potentially affect the supply chain for prototyping projects.
Joining Difficulties:
Welding titanium can be intricate, and special precautions are needed to prevent contamination and maintain the integrity of the welds.
Understanding the characteristics, advantages, and limitations of titanium is essential in making informed decisions for selecting the right metal for prototyping needs. This knowledge empowers designers and engineers to harness titanium’s strengths while mitigating its challenges to create innovative and exceptional prototypes.
Exploring Aluminum
Aluminum is a ubiquitous and versatile metal. It has revolutionized numerous industries with its remarkable properties and adaptability. In this guide, as we uncover aluminum’s diverse applications and examine why it remains a sought-after choice for prototyping needs.
Characteristics and Properties of Aluminum:
Lightweight Champion:
Aluminum is one of the lightest metals available for prototyping. It offers low density which is its unique feature as compared to other materials. Its ability to reduce weight while maintaining adequate strength is particularly advantageous in many applications.
Excellent Strength-to-Weight Ratio:
Despite its lightweight nature, aluminum exhibits impressive strength. That makes it suitable for prototypes requiring both durability and weight efficiency.
Corrosion Resistance:
Like titanium, aluminum forms a protective oxide layer when exposed to air. Due to which it offers remarkable corrosion resistance that enables its use in various outdoor and marine applications.
High Thermal and Electrical Conductivity:
Aluminum’s excellent thermal and electrical conductivity make it an ideal choice for prototypes requiring heat dissipation or electrical conductivity.
Advantages of Aluminum in Prototyping:
Cost-Effectiveness:
Aluminum is an economical alternative for prototyping projects especially when large quantities are required. As aluminum is comparatively more affordable than titanium.
Easy Machinability:
Aluminum’s relatively soft nature and excellent machinability allow for efficient and precise fabrication processes. That reduces manufacturing time and costs.
Widely Available:
Aluminum is abundantly available worldwide, ensuring a stable and consistent supply chain for prototyping projects in various locations.
Versatility in Industries:
Aluminum is a popular choice for cross-industry prototyping needs. It finds its applications in an array of industries like automotive, consumer electronics, construction, packaging, etc.
Limitations and Considerations for Aluminum Usage:
Lower Strength than Titanium:
As aluminum is strong for its weight. It generally falls short when compared to titanium’s impressive strength-to-weight ratio. This may limit its application in certain high-stress or aerospace-related prototyping projects.
Corrosion Vulnerability in Certain Environments:
Although aluminum boasts corrosion resistance, it may not be as resilient as titanium in highly corrosive or extreme environments. That necessitates careful consideration for specific use cases.
Weight Reduction vs. Strength Balance:
In some cases, achieving the perfect balance between weight reductions and maintaining sufficient strength may require additional design considerations when using aluminum.
Anodization Challenges:
As aluminum can be anodized to improve its surface properties. This process may add complexities and costs to the prototyping process.
Exploring aluminum’s characteristics, advantages, and limitations enables designers and engineers to harness its potential effectively. By understanding its unique properties, one can make perfect decisions to leverage aluminum’s strengths and navigate its limitations. It will ultimately results in efficient and cost-effective prototypes creations for a wide range of applications.
Comparing Titanium and Aluminum
Choosing the right lightweight metal for prototyping needs entails a comprehensive comparison between two prominent contenders: Titanium and Aluminum. Let’s closely examine the critical aspects that set these metals apart and influence their suitability for various prototyping applications.
Weight and Density Comparison:
Titanium:
Titanium is renowned for its exceptional strength-to-weight ratio. It offers a remarkable strength while remaining significantly lighter than most metals. Its low density contributes to reducing the overall weight of prototypes. Which making it ideal for applications where weight reduction is paramount.
Aluminum:
As a lightweight champion, aluminum boasts an even lower density than titanium. It is one of the lightest metals available. It provides excellent weight reduction potential for prototyping projects without compromising strength.
Strength and Durability Comparison:
Titanium:
Titanium’s outstanding strength and rigidity make it an excellent choice for prototypes requiring superior durability. It exhibits exceptional resistance to deformation under pressure. It is well-suited for high-stress applications and industries like aerospace and defense.
Aluminum:
While aluminum is strong for its weight. It generally has a lower strength compared to titanium. It is ideal for applications where weight reduction is crucial. But its use in highly demanding environments or industries may require additional considerations for structural integrity.
Cost Analysis: Titanium vs. Aluminum:
Titanium:
Titanium’s exceptional properties come with a higher price tag compared to aluminum. The cost of raw titanium materials and its challenging extraction and refinement process contribute to its relatively higher price. Due to this reason, it is less cost-effective for some prototyping projects.
Aluminum:
Aluminum’s widespread availability and ease of extraction contribute to its cost-effectiveness. It is generally more affordable than titanium. Mostly preferred for projects with budget constraints or when large quantities are required.
Machinability and Formability Differences:
Titanium:
Titanium’s high strength and low thermal conductivity can pose challenges during machining. Specialized tools and techniques are often required to shape and fabricate titanium components. It adds complexity to the manufacturing process.
Aluminum:
Aluminum’s excellent machinability and formability are key advantages in prototyping. It can be easily molded, extruded, and machined. That leads to faster production times and reduced manufacturing costs.
As both titanium and aluminum offer unique strengths and advantages. The selection between the two largely depends on the specific requirements of the prototyping project. Engineers and designers must carefully evaluate the trade-offs in weight, strength, cost, and manufacturability to make an informed decision that aligns with the project’s goals and constraints.
By understanding the nuances of these metals, one can harness their potential and create prototypes that truly excel in their intended applications.
Conclusion:
As both titanium and aluminum offer unique strengths and advantages. The selection between the two largely depends on the specific requirements of the prototyping project. Engineers and designers must carefully evaluate the trade-offs in weight, strength, cost, and manufacturability to make an informed decision that aligns with the project’s goals and constraints.
By understanding the nuances of these metals, one can harness their potential and create prototypes that truly excel in their intended applications.