The types of abrasion commonly seen in cnc machine shops include run-in wear, hard grain wear, surface fatigue wear, thermal wear, phase change wear and corrosion wear.
01
Run-in wear is the wear and tear that occurs under normal load, speed and lubrication conditions of machinery, which generally develops slowly and has little impact on the quality of cnc processing in the short term.
02
Hard grain wear is caused by abrasive grains dropped from the part itself or from outside sources entering the machine tool, mixing into the machining area and being subjected to mechanical cutting or grinding, causing damage to the part, which has a serious impact on machining quality.
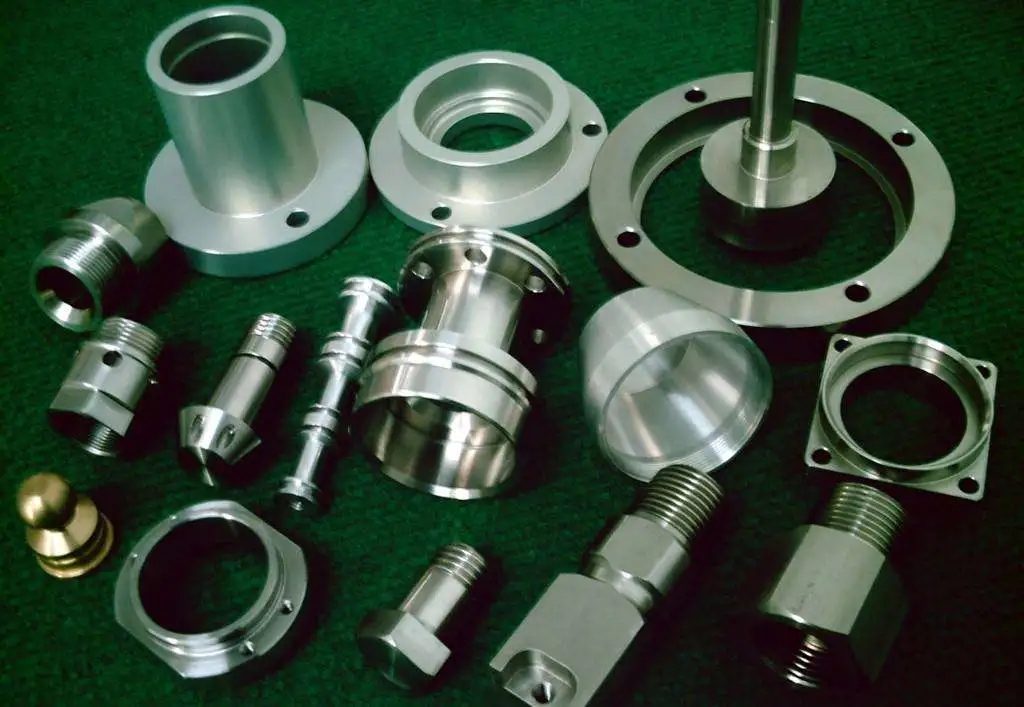
03
Surface fatigue wear is the damage to parts caused by tiny cracks or ban-spot pits in machinery under the action of alternating loads. This type of wear is usually closely related to factors such as pressure magnitude, load characteristics, part material, and size.
04
Thermal wear is the effect of heat generated by the friction process on the parts, which causes the parts to temper and soften, burn and crease. This type of wear usually occurs at high speeds and high pressures in sliding friction, and is more destructive in nature with accidental wear.
05
Corrosion wear is a chemical action, i.e. chemical corrosion causes wear and tear. When the surface of the part is in contact with acid, alkali, salt liquids or harmful gases, it will be chemically eroded, or the surface of the part combined with oxygen to generate hard and brittle metal oxides that are easy to fall off and make the part wear.
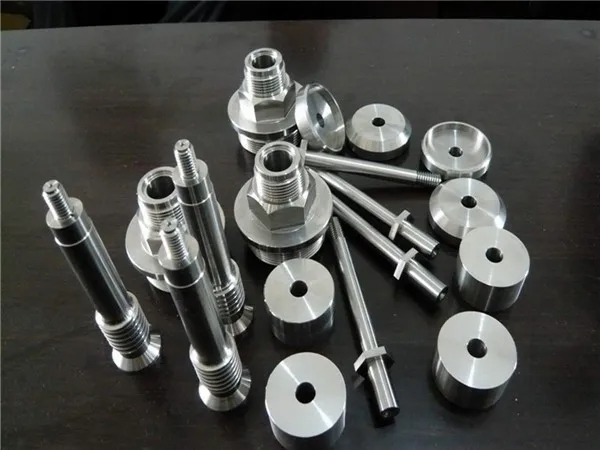
06
Phase change wear is the work of the parts under high temperature for a long time, the metal tissue grain on the surface of the parts become heated, the grain boundary around the oxidation, resulting in a small gap, making the parts fragile, wear resistance decreased, resulting in parts wear.